I built the wheel house door out of Aluminum. Given how exposed the wheel house is, I thought Aluminum would offer me a more tough door. Now that it's all said and done, I do think the aluminum door is more robust than my wooden salon door. The salon door, at two inches thick is for sure a tough door, but the all welded Aluminum door appears to be pretty tough given the weight of it.
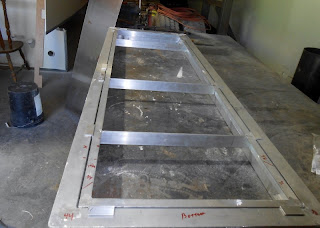
The first decision I had to make on the wheel house door build was how to build the frame. I found a piece of 2 x 6 x 1/4 " angle at the scrap yard and ripped the six inch side to 4" to match my 4" wheel house frame depth. The angles on the rough opening are a degree off of 90, so a little fitting had to be done before I could tack the frame together. I guess at this point I should say that I TIG welded the wheel house door. The frame was assembled using miter's, with all the cuts being made with my miter saw... you gotta love Aluminum. Once the frame was fit in to the opening, I built the actual door frame using some 1" x 2" angle and some 2" flat bar for internal framing.
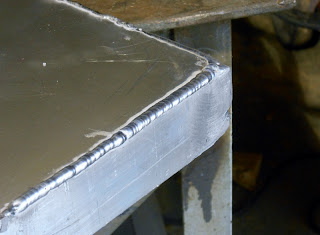
I had the hinges in the shop, so figuring out the reveal of the door was not too big of a deal.
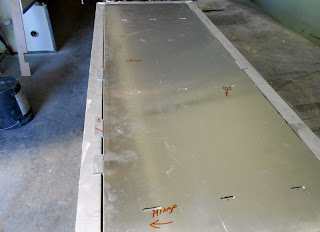
With hindsight being 20/20, I wish I had used a hinge that did not require a mortise. I ended up having to create a mortise for the hinge in the door, and while not a deal killer for the success of the job, it was sort of a pain.
The flat bar cross member framing of the door was laid out for a couple of strategic reasons. Two of the cross members were laid out as to house the Trioving lock assembly. To make all the lock assembly housing hidden yet removable, I added an internal plate to bolt the lock assembly in to. Trioving bores four holes through this composite lock assembly housing for just the purpose I needed. The four bores are the same size needed to tap a 1/4-20 thread so one can attach the lock housing assembly to the door. On my wooden salon door, I created a mortise, then epoxied the lock assembly housing in to the mortise. The other two flat bar cross members were installed in the locations where my inside door dogs will be bolted to the interior door skin. In order to keep the door skin flat, I had to weld a few braces in to the door frame perpendicular to the cross members.
Aluminum is great material to work with, but controlling movement due to the immense heat created by TIG welding is a challenge. Taking your time and paying attention to the heat is crucial. I also found that by clamping blocks of heavy stainless steel under my welds and along side of weld areas helped the heat sink in to the blocks and keep things under control. My external door skin was .090.
Because I had always intended on painting the door, I ground all the welds on the exterior of the door and on the frame. Once I had the welds ground flush, and repaired a few welds that failed as a result of grinding, I sand blasted the door and frame.
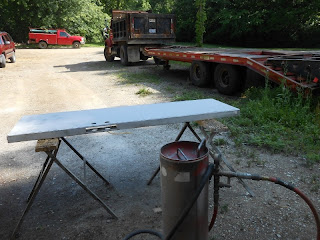
On As per advice from my paint vendor, I conditioned the aluminum with some material I applied with a spray bottle. The conditioner had to sit on the metal for 15 or 20 minutes, then I hosed the metal clean and let it drip dry. My paint guy said the conditioner is good for 24 for hours, so after baking in the sun for a few hours, I hung the door from some lines and gave it two coats of epoxy primer along with the frame. After priming the door, I faired the ground edge of the door first using West epoxy mixed with fairing compound, then finished with Rage filler sanded to 320 grit. Spot painting two coats of primer on the filler to seal it, then three or four coats of acrylic urethane top coat and the door was ready for assembly.
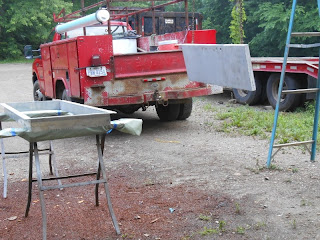
I pre drilled the frame for 1/4" screws, and will not final install the door until the super structure is landed at the launch site later this summer. I also have only installed a temporary stop as I'm still undecided on what type of gasket I"m going to use to seal the door to the stop. Once I decide on the type of gasket and how much room the gasket requires, I'll bolt the door stop to the frame. The door stop will be hardwood and will extend out the the edge of the door frame to also catch the interior finish wall sheathing. Another important build part of my wheel house door is that I decided that the interior skin of the door will be Cherry to match the wheel house finish wood. Because the doors interior skin will be plywood, I bolted firing to the cross members.
After I land the super structure to the hull and have all he weld zones painted, I'm going to have the spray foam insulators back to spray all those areas. When the spray contractor is on site, I'm going to have him spray foam the inside of the door before I install the plywood interior skin.
Now that the wheel house door is complete along with the salon door, the last piece of being able to secure the boat from weather and other undesirables is now complete. I've pretty much stopped working on finish type things of the build, and am now focusing on getting things ready to move her out of the barn. Getting her in the water next Spring is the plan, and believe it or not, that date is fast approaching. It's time to it done.
I started to add some You tube videos if anyone's interested. The videos are pretty lame, but hopefully I'll start improving on them. I'll post a link soon.
Cheers