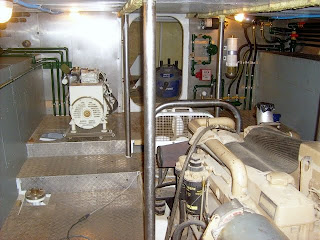
The fuel transfer system resides in the engine room on the port side of the boat against the aft water tight bulkhead. I've put a huge dent in the amount of work building the transfer system, and there is enough of the system completed for me to blog about. I want to use JIC fuel fittings on the lines between the intake manifold, the filter, the pump and the distribution intake, so I have to wait until Tuesday to get the lines made. Once I run the wire for the disconnect switch and get those lines fabricated, I'll be able to pump fuel from tank to tank.
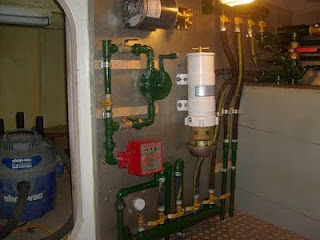
I have four fuel tanks on board for a total of between 1300 - 1400 gallons. Three of the tanks will be used for storage, and the fourth tank will be a 200 gallon "day" tank that will be used to feed the main engine and the 10kw generator. The fuel transfer system is completely independent from the fuel delivery system which feeds the machinery out of the 200 gallon day tank.
Every day we are traveling on the boat we will manage our fuel by transferring fuel from tank to tank and making sure the day tank is full. As the fuel is transferred it will be filtered through a 1000 series Racor filter that will also remove water. The fuel that leaves the day tank to feed the machinery, will again pass through another Racor filter before being filtered by the factory filters on the main engine and generator. I have a mechanical flow meter in the transfer system that will be the primary way we keep track of how much fuel we have left and how much we are using. Once I fill the tanks and have some sort of base line for tank capacities, we'll use a log book to track fuel usage along with a flow meter on the main engine and dip sticks for the tanks.
The transfer system's pump is a rotary vane pump driven by a 120 volt 1/2 hp motor. The motor is continuous duty rated motor so I don't have to worry about run time. The pump and motor can move 220 gallons per hour which exceed the 180 gallon flow rate of the 1000 series Racor filter. I don't know if I need to put a gate valve on the pump to choke it down or if the Racor will do that for me. The motor pulls about 7 amps, and I'll have it wired in to the inverter circuit so I don' have to worry about having shore power or the generator running if I want to transfer fuel. The rotary vane pump is self priming and is pretty close to bullet proof. This is very long life pump made by Procon that
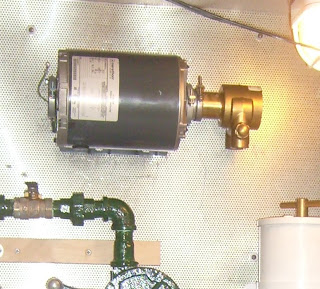
should give me a long life of reliable service. If for some reason the pump or motor fails me, I have a manual pump plumbed into the system that will handle our fuel transfer needs. I got the idea of the manual pump from a careful builder doing a fine job on building their 55 footer. You can check out Peter and his families boat building blog here:
building koloa . If the manual transfer pump fails me I can use one of the four drain valves and another type of manual pump to move fuel. If I don't feel like doing that, I can block the vents and carefully use my air compressor
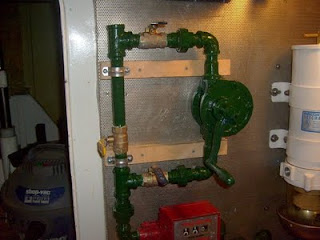
and a regulator to push fuel from tank to tank using the transfer manifolds.
When transferring fuel,the fuel is pulled for one of the four tanks via a four port manifold. After the fuel goes through the filter, pump, and flow meter it is then pushed through a distribution manifold with five valved ports. Depending on what combination of valves is opened is how the fuel will find it's way to the desired tank. On the five valve distribution manifold, four valves are for directing fuel to any of the four tanks, and the fifth valve is used for pumping fuel to some place else. If I ever have to give fuel to a stranded boat or get fuel off of the boat for some other reason, the fifth valve will be the way to do it. I actually have a sixth port of the distribution man
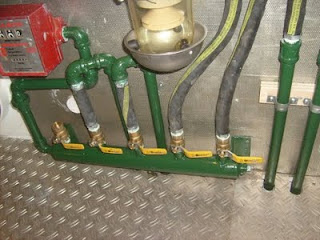
ifold since I did not know from which end I was going to be feeding the m
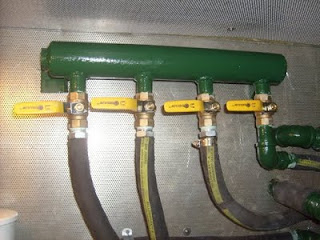
anifold. I have the sixth port plugged. All the flexible fuel line I've been using in the engine room is Coast Guard approved marine fuel hose.
This was a pretty involved project, but I'm for sure on the tail end of it and will have it operational within a few days. If I were to do it all over again, I would have paid more attention to how I was going to run the piping while I was building the tanks. A plan would have been nice, but you know how that goes. Stainless steel pipe would have been another good thing, but since I'm on a shoe string budget, painted steel pipe will have to do. All the piping has been air tested from the manifolds, through the tanks to the deck fills and vents. I'll probably put 30 gallons of fuel in the system and start moving fuel around to clean the tanks. The next part of the fuel system to build is the delivery system and returns for the main engine and generator. I'll be starting on the delivery system this week.